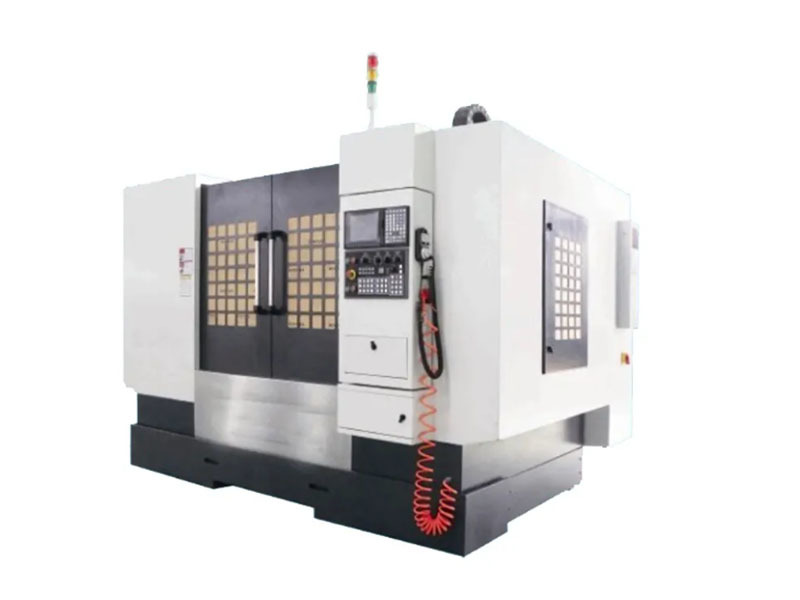
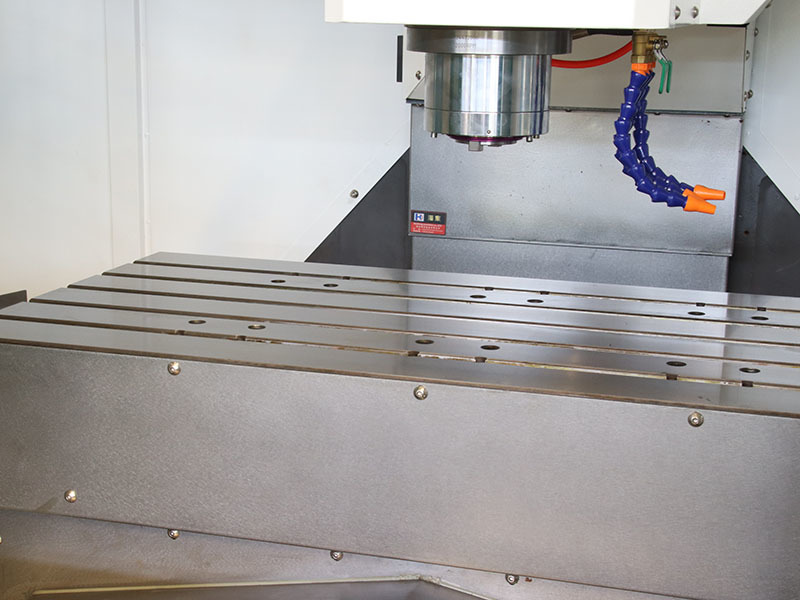
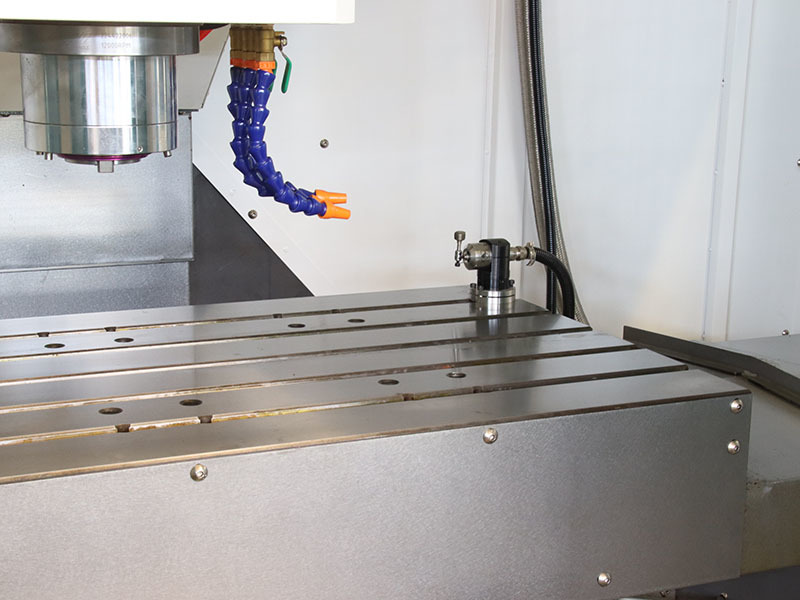
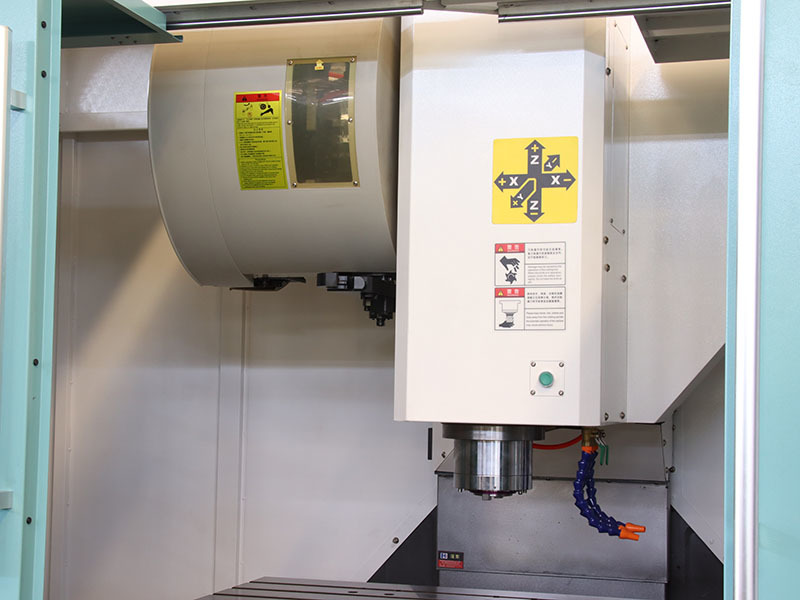
VMC1370 vertical CNC machining
Category:
Keyword:
VMC1370 vertical CNC machining

Telephone:13793702928
- Product Detail
- Feature
- Accessories
-
- Commodity name: VMC1370 vertical CNC machining
one. Function and feature description
1 Overall layout of machine tools
The VMC1370 vertical machining center adopts a vertical frame layout. The column is fixed on the bed. The spindle box moves up and down along the column (Z direction), the slide moves longitudinally along the bed ( Y direction) , and the workbench moves laterally along the slide ( X to) structure.
Large parts such as the bed, worktable, slide, column, spindle box, etc. are all made of high-strength cast iron materials, and are shaped using resin sand technology, and are treated twice with aging treatment to eliminate stress. These large parts are designed using SW and Ansys optimization to improve the stiffness and stability of the large parts and the entire machine, effectively suppressing the deformation and vibration of the machine tool caused by cutting forces.
2Drag system
The X and Y axes use linear guides, which have the characteristics of high precision, fast feed speed, and heavy load , improving the movement accuracy of the equipment . The Z-axis uses rectangular guide rails with high rigidity and low noise. The guide rails quenched and adopt internationally advanced guide rail plastic technology to have low friction coefficient, rigidity, reliability and strong stability.
The Z-axis servo motor has an automatic brake function. In the event of a power outage, the brake can automatically hold the motor shaft tightly so that it cannot rotate, which plays a role in safety protection.
3 spindle group
The spindle group is produced by professional manufacturers in Taiwan and has high precision and high rigidity. The bearings adopt P4 grade special bearings for spindles . After the entire set of spindles is assembled under constant temperature conditions, they pass dynamic balance correction and running-in tests, which improves the service life and reliability of the entire set of spindles .
The spindle can achieve stepless speed regulation within its speed range. The spindle is controlled by a built-in encoder in the motor, which can realize spindle orientation and rigid tapping functions.
4 tool magazine
A robot tool magazine is installed on the side of the column. When changing tools, the cutterhead is driven and positioned by a roller cam mechanism. After the spindle reaches the tool changing position, the robot tool changing device (ATC) completes tool return and tool feeding. ATC is gear hobbing . The cam mechanism, after being preloaded, can operate at high speed and noiselessly, making the tool changing process fast and accurate.
5 cutting cooling system
Equipped with a large-flow cooling pump and a large-capacity water tank to fully ensure circulating cooling. Cooling pump power: 0.4Kw, pressure: 1.2bar.
The end face of the spindle box is equipped with a cooling nozzle, which can be water-cooled or air-cooled, and can be switched at will. The cooling process can be controlled through M code or control panel.
Equipped with a cleaning air gun for cleaning machine tools.
6Pneumatic system
The pneumatic triplex can filter impurities and moisture in the air source to prevent impure gas from damaging and corroding machine tool components. The solenoid valve group is controlled by the PLC program to ensure that spindle tool unclamping, spindle center air blowing, spindle tool clamping, spindle air cooling and other actions can be completed quickly and accurately.
7Machine tool protection
The machine tool adopts a protective room that meets safety standards, which not only prevents coolant from splashing, but also ensures safe operation and a pleasant appearance. Each guide rail of the machine tool has a protective cover to prevent chips and coolant from entering the machine tool and protect the guide rails and ball screws from wear and corrosion.
8 Lubrication system
The guide rails and ball screw pairs are all lubricated by centralized automatic thin oil. Each node is equipped with a quantitative oil separator, which regularly and quantitatively injects oil into each lubricating part to ensure that each sliding surface is evenly lubricated, effectively reducing friction resistance and improving movement. The accuracy ensures the service life of the ball screw pair and guide rail.
9chip removal system
The iron chips generated during the machining process fall directly onto the guard room. The internal bevel structure of the guard allows the iron chips to slide smoothly into the chip conveyor, and then the iron chips are transported to the chip collecting car through the spiral chip conveyor. It is simple, practical and Good economy.
10Machine tool working conditions
(1)Power supply: 380V±10% 50HZ±1% three-phase alternating current
(2)Using temperature: 5℃-40℃
(3) Optimal ambient temperature: 15℃-25℃
(4) Relative humidity: 40-75%
(5) Air source pressure: 0.5-0.7Mpa
(6) Air source flow: 350L/min
two. Main specifications and technical parameters
VMC1370
unit
workbench
working desk size
1400×700
mm
maximum allowable load
1200
k g
T- slot size
140-22-5
mm ×pcs
processing
scope
Maximum travel of worktable - X axis
1300
mm
Maximum travel of slide - Y axis
700
mm
Maximum spindle travel - Z axis
700
mm
Spindle end face to
Work surface distance
maximum
860
mm
smallest
160
mm
Distance from spindle center to guide rail base surface
780
mm
Spindle
Taper Hole (7:24)
BT 50
RPM range
50~6000 _
r/min
Maximum output torque
143
Nm
Spindle motor power
11
kw
Spindle transmission mode
Synchronous toothed belt
Knives
Tool holder model
MAS403BT50
Pull nail model
MAS403 BT50-Ⅰ
Feed
Fast-moving
X- axis
twenty four
m/min
Y axis
twenty four
Z axis
18
Feed rate
1-8,000 _ _
mm /min
Three-axis drag motor power
2.5/2.5/2.5
kw
*Tool magazine
Tool magazine form
Disc type .
Knife selection method
Pre-selected knife
Tool magazine capacity
twenty four
Bundle
Maximum tool length
300
mm
Maximum tool weight
18
kg
Maximum cutterhead
diameter
full knife
Φ112
mm
Adjacent empty knife
Φ200
mm
Tool changing time
3
s
positioning accuracy
JISB6330
JB/T 8771.4-1998
mm
X- axis
± 0.0 05/300
0.020
Y axis
± 0.0 05/300
0.015
Z axis
± 0.0 05/300
0.015
mm
Repeatability
X- axis
±0.005
0.012
mm
Y axis
±0.005
0.010
Z axis
±0.005
0.010
mm
Machine weight
7000
kg
Product Video
FAQ

Who are we?

We are located in Shandong, China and have been selling to the domestic market since 2014 (70.00%), Northern Europe (10.00%), Eastern Europe (10.00%), Africa (5.00%), the Middle East (3.00%), and South America (2.00%). Our office has a total of 51 to 100 people.

How do we ensure quality?

Always provide pre production samples before mass production; Always conduct final inspection before shipment;

What can you buy from us?

CNC turning and milling compound lathe, CNC lathe, CNC vertical machining center, CNC vertical milling machine, CNC vertical lathe, gantry machining center.

Why should you purchase from us instead of other suppliers?

We specialize in manufacturing these products for 20 years and have obtained ISO 9001 certification; Ce certification; EAC certification.

Do you have a physical factory?

Yes, we are a CNC lathe manufacturer from Tengzhou City, Shandong Province. We have a professional technical team, sales team, and after-sales team.

Can you customize the machine?

Yes, we integrate design and development together, with experienced engineers and assembly technicians.

What services can we provide?

Accept delivery terms: FOB, CFR, CIF, EXW; Accepting payment currency: USD, CNY; Accepting payment types: T/T, L/C, Western Union remittance; Language: English, Chinese

May I visit your factory?

Okay, we warmly welcome you.
Partners


Related Products
Get a free quote
To: All protection